Piezoelectric effects for the suppression of material stresses
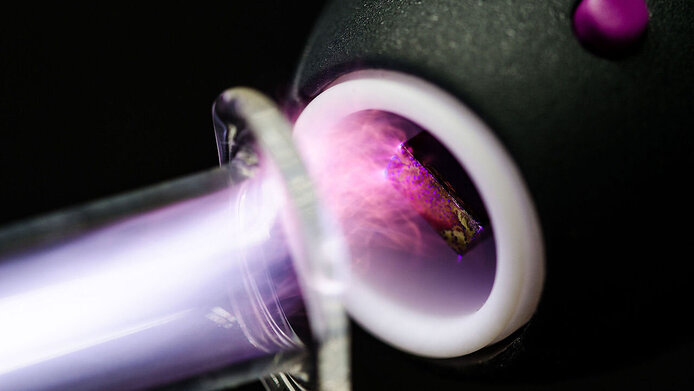
High levels of mechanical stress reduce the lifespan of construction components. This is true for all types of materials; exposure to mechanical stress is a crucial factor in the duration of their lifespan. When stresses are combined with vibrations they have a particularly negative impact on durability. Intelligent materials that can actively counteract such effects have been available for special applications for some years now. The solution applied here involves a very sophisticated trick of physics: the so-called piezoelectric effect, that is the generation of an electrical charge through deformation, can be used to actively suppress these forces. However, piezoelectric materials are also subject to forces which reduce their durability and finding a way of changing this is the challenge that scientist Jürgen Schöftner has set himself.
Vibrations and stresses
A particular characteristic of piezoelectric materials plays a key role in Schöftner's research: "A distinctive feature of piezoelectric materials is their special combination of physical properties. This is responsible for the fact that an increase of mechanical stress can arise even if the mechanical deformation of the material, which was caused by external forces, has already abated." Such local increases in stress have a negative effect on the durability of the material and Schöftner aims to reduce them. As he explains, he is entering uncharted scientific territory here: "The research carried out in recent years in this field, which is known as 'structural control', focused mainly on the reduction of vibrations and deformations. These methods are so far well understood. However, the findings on the avoidance of vibrations are of no help when it comes to the avoidance of mechanical stresses. New methods are needed here and we plan to develop the basis for them." The first stage of Schöftner's project involves the analysis of the so-called constitutive relations for piezoelectric materials. This will enable the deduction of formulations for possible stress suppression in the three-dimensional space. He will then also calculate the basic differential equations for the stress. The aim of these basic calculations is to find workable concepts for the suppression of stresses in so-called lean components.
Passive regulation – Active energy harvesting
However, Schöftner is looking even further into the future in his project: "Piezoelectric materials can actually be used to harvest energy. The kinetic energy of a component is transformed into electrical oscillations and, therefore, neutralised. If the piezoelectric material is integrated into an electric network, the charge generated through the mechanical deformation can also be transmitted to a suitable electrical storage medium." The long-term aim is to design an electrical network for a particular vibrating piezoelectric structure which, depending on requirements, regulates a mechanical stress under a certain level or transforms the vibrational energy into electrical energy through storage. This would require a smart circuit which consists of an active circuit for the stress regulation and a passive circuit for the energy harvesting. Ideally, the mechanical stress would be regulated from a critical stress level – otherwise, vibrational energy would be converted into usable electrical energy. However, some basic homework will have to be done before such systems become a reality. Thus, in his project, Schöftner is working on the optimal distribution of the electrodes, the sheet resistance and the electrical network in such a system. "The potential offered by such passively controlled materials is huge – however, before they can actually be used, we must obtain some basic information about the optimisation of these materials. This is precisely what we are doing in this FWF project," adds Schöftner.
Personal details Jürgen Schöftner has been a researcher at the Institute of Technical Mechanics at the Johannes Kepler University Linz since 2011. He is an expert in modelling and control of mechatronic problems.