Feeding plants with electricity
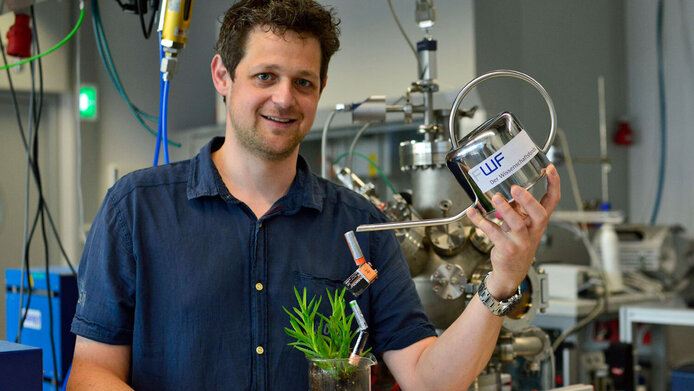
The importance of ammonia (NH3) is not often a topic of public debate, but it is one of the most widely produced and most important substances for a variety of applications. Every year, almost 150 million tons of ammonia are produced worldwide. Ammonia is used as a refrigerant or in the production of plastics – but most of it is goes into the production of synthetic fertilizers. Plants need the nitrogen these fertilizers contain for growth and photosynthesis. For this reason, ammonia has become an indispensable part of our modern society. Whereas one of its components – nitrogen – is present in large quantities in our atmosphere as N2 molecule, the synthesis of ammonia also requires hydrogen (H2) as a starting material. Currently, hydrogen is mostly produced with the help of fossil resources. In addition, fossil fuels are also used for the energy-intensive production of ammonia from N2 and H2. Alexander Opitz and his team at the Vienna University of Technology (TU Wien) are seeking to develop a sustainable alternative in their project "Feeding plants with electricity."
“We started this project because we can harness our expertise in electrochemistry in order to develop a new form of ammonia production that uses renewable energy and base materials,” explains Alexander Opitz. “One of the biggest challenges is to break up the extremely stable nitrogen molecules in the atmosphere and combine them with hydrogen atoms to produce ammonia.”
The research project “Feeding plants with electricity”, set to run from 2021 to 2024, is being funded by the FWF under its 1000 Ideas Program for particularly innovative research.
The project aims to develop a new electrochemical process for ammonia production which is based on sustainable energy and raw materials.
Ammonia (NH3) consists of a nitrogen atom that is bonded to three hydrogen atoms. Nitrogen atoms like to combine with another nitrogen atom and the resulting N2 is a very stable molecule. In the early 20th century, two chemists developed the Haber-Bosch process which uses pressures of several hundreds of bar and temperatures of several hundred degrees Celsius to break up the nitrogen molecules for ammonia production. The vast amounts of energy required by this chemical process result in the production of ammonia alone being responsible for 1.4 percent of global carbon dioxide emissions and around 1 percent of global energy consumption. Hence, there is enormous savings potential. Given that this process is only economically viable at a large scale, global ammonia production is concentrated in only around 100 industrial plants. This is where Alexander Opitz's research comes in.
Pressure through voltage
Opitz is conducting research, supported by postdoc Maximilian Weiss, PhD student Melanie Anstiss and graduate student Christian Wimmer, to find an alternative way of producing ammonia. “Instead of using a lot of energy to generate hydrogen gas at a pressure of hundred bar so that it can bind to nitrogen, we use the processes at the electrodes of electrochemical cells – comparable to electrolysis,” explains Opitz.
In electrolysis, an electric current forces a chemical reaction at an electrode. “In our experimental setup, we use a special ceramic electrode material that we produce ourselves. Unlike many other materials, it can conduct both negatively charged electrons and positively charged protons – the nuclei of hydrogen atoms. In combination with a proton-conducting electrolyte between the electrodes, we can pump hydrogen through the electrochemical cell and influence the effective pressure at the electrode by means of the applied voltage.”
In the experiment, the research group first brings hydrogen gas to one side of the ceramic electrolyte. At the electrode located there, the hydrogen atoms lose their only electron and are left with only the atomic nucleus – a single proton that can move within the electrolyte. The applied electrical voltage then forces the positively charged protons to the other side of the electrolyte, where the second electrode is located. This second electrode, which consists of the special ceramic material, creates the high effective hydrogen pressure that is required for the production of ammonia. “That's the trick in our project,” explains Opitz. “We can put hydrogen under high pressure by simply applying electrical voltage which can come from renewable sources.”
In addition, the surface of the cathode material is equipped with a catalyst, a specially selected material that helps to break up the stable atmospheric nitrogen molecules and combine them with hydrogen.
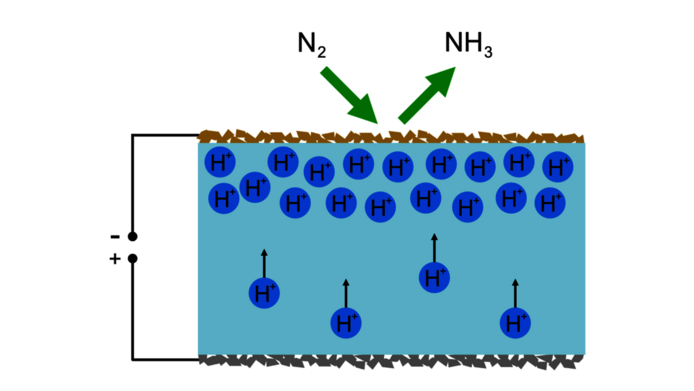
© Thomas Zauner
Sustainable raw materials and decentralization
“Many problems had to be solved, and we still have a lot of work ahead of us,” notes Opitz. “For example, we first had to find an effective method for easy measurement of the concentration of hydrogen in our ceramic materials in the laboratory. We achieved it thanks to a successful collaboration with colleagues working in analytical chemistry at TU Wien.”
One of the next steps will be the selection of the best catalyst, and the researchers also want to incorporate a sustainable source of hydrogen into their process. “So far, most of the hydrogen has been obtained from fossil natural gas. We would like to expand our process to produce the hydrogen, which is then pumped through our electrochemical cell, directly from water,” says Opitz.
Research into electrochemical ammonia production will continue for some time to come, but Opitz and his team are highly motivated and already have potential areas of application in mind. “Our approach could be used to make other chemical reactions with hydrogen more sustainable. We can also use it to enable decentralized ammonia production, as our technology allows for relatively easy up- and downscaling. Farmers, for instance, could use a small electrochemical reactor to produce the ammonia they need locally for their fertilizer. In this way, they could feed their crops with nitrogen from their own production.”
Personal details
Alexander Opitz is head of the Electrochemical Energy Conversion research group at the TU Wien. In his research, he has primarily been focusing on the in-situ characterization of mixed ionic and electronic conductive materials and the investigation of so-called exsolution electrodes. In 2017, he pursued this topic at the Massachusetts Institute of Technology (MIT) as a visiting scientist. In January 2022, Alexander Opitz completed his professorial qualification and was appointed associate professor.