Better injection systems for diesel engines
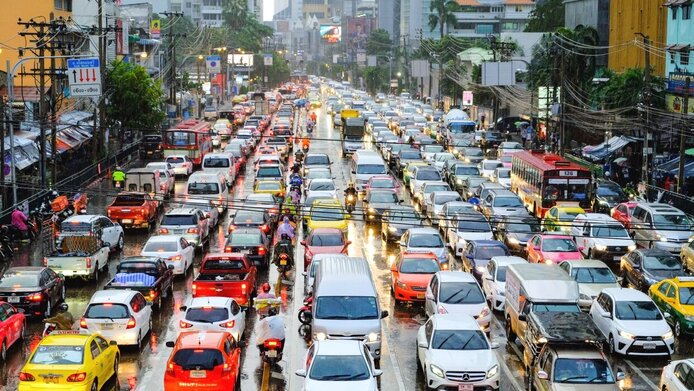
Diesel engines are currently the object of strong criticism because of their emissions. Nitrogen oxides and soot impair the image of the “clean” diesel engine. Whilst the share of nitrogen oxides can be reduced only by adding chemicals or by lower combustion temperatures and a concomitant loss of torque, the generation of soot depends on the quality of the combustion process itself. The times are long gone when it was enough to simply inject a little fuel at a given point: in most cases the injection nozzle first discharges smaller quantities of diesel fuel. Once these have ignited, the rest of the fuel is added. All of that needs to happen in a fraction of a second and requires high precision injection nozzles in common rail diesel engines. Magnetic valves are often too slow, which is why piezo crystals are used in this case. These crystals have hitherto been used by clock or watchmakers or in electron microscopy where every millionth part of a millimetre counts. Headed by the material scientist Marco Deluca, a team of researchers from the Materials Center Leoben (MCL) has now managed to develop the basis for making the piezo elements used in the automotive industry more effective and reliable. In a project funded by the Austrian Science Fund FWF the scientists probed deeply inside these crystals.
Better than quartz
The relevant property of piezo crystals is the fact that they expand when electric voltage is applied to them. Conversely, they generate voltage when subjected to mechanical stress. Hence, an electrically activated piezo crystal can open a valve. The most well-known material with this property is quartz, which was used typically as a clockwork generator. The automotive industry uses ceramic materials that are known as ferroelectric and have slightly different properties, explains Marco Deluca in the interview with scilog: “There’s a difference compared to quartz. If you exert pressure you create electrical voltage. In quartz, this property cannot be modified, but with ferroelectric materials it is possible to influence the direction of the material’s expansion.” Whereas the atoms in a quartz crystal are very ordered, ferroelectric ceramics consist of tiny so-called domains that are smaller than one millionth part of a millimetre. If sufficiently high voltage is applied these domains go through a cooperative reorientation. “Because of the domains’ reorientation the same voltage results in a greater expansion than with quartz-like materials that are merely piezoelectric”, notes Deluca. This greater elongation is of prime importance for injection nozzles.
Investigations with laser and x-rays
In the automotive industry, common rail injection nozzles with piezo injectors have been used for several years, but there are some technical problems. The engineers struggle with cracks in the ceramic elements which is why these elements are installed with a certain amount of pre-stress. “In addition it has been observed that performance is improved if the actuators are installed in the engine under a load of about 50 mega pascal. But the manufacturers did not know why”, reports Deluca. It was one of the objectives of the project to gain a better understanding of this effect. “In order to do that we investigated commercially available piezo actuators in action using Raman laser spectroscopy and x-rays.” Such investigations require high-energy x-rays that can be precisely focused. They are generated in particle accelerators similar to the ones used at the CERN nuclear research centre. These rays can penetrate the material and provide an exact picture of the positions of the atoms.
For his project, Deluca cooperated with the North Carolina State University, which has access to a particle accelerator (Advanced Photon Source) where the measurements were conducted. “Raman spectroscopy, on the other hand, shows the average lattice orientation, i.e. the orientation of the domains at the level of micro-metres and thereby provides additional information on a different scale. In Leoben we already have such Raman equipment”, says Deluca. Investigations showed that mechanical pre-stressing changes the orientation of the domains: the pre-stressing orders the domains in a certain direction perpendicular to the electric field axis. Once they are electrically actuated, more domains can change phase than is possible in the absence of mechanical pre-stressing. “You thereby create greater changes in the length of the material”, notes the researcher. On the basis of this knowledge they were able to determine the optimum pre-stressing for technical applications.
Avoiding cracks
Another objective of the project was to avoid the formation of cracks. “Crack formation can be stopped if you can control the original orientation of the ferroelectric domains.” To do that one needs to first capture the direction in which the domains are oriented. “It was one of the goals of our project to find and fine-tune methods that can measure the orientation of ferroelectric domains.”
Many possible applications
These insights are already being used by industry, reports Deluca. Not only the automotive industry is interested in this development, there are other technology sectors that also opt for piezoelectric methods. “In the end there’s always one problem: which orientation is best for this application? How can the orientation of domains be changed? And under how much strain can they be put without being destroyed? This will be primarily important for energy harvesting or energy self-sufficient sensors.” There are also potential medical applications. “In all of these fields, energy is generated from a deformation process. The material we analysed can be used for that purpose”, declares Deluca.
Personal details Marco Deluca is a material scientist in the microelectronics group of the Materials Center Leoben (MCL). He heads the research group for functional materials, which is particularly interested in the structural properties of semiconductors and ceramics, as well as for the deposition of thin oxide layers by means of low-cost spray methods. In addition, Deluca currently is in charge of another FWF funded project about relaxor materials, a non-ordered type of ferroelectric ceramics. In this project, which runs until the end of 2019, the researchers use a combination of Raman spectroscopy and atomistic modelling in order to determine structure-property relationships in relaxors. The researchers aim to uncover the atomistic cause of the relaxor properties. Marco Deluca is also a private lecturer at the Montanuniversität in Leoben.
Publications