A new drive system for wheelchairs
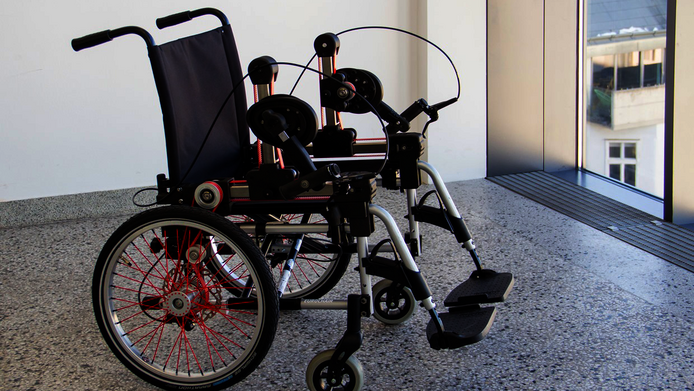
For people with a mobility handicap, wheelchairs are the most significant means for getting about. Wheelchairs with a manual drive, usually involving handrims attached to the wheels, remain important, but they have several disadvantages. On the one hand, their efficiency level is limited to just ten percent, and, on the other, they require extreme positions for the arm and hand joints, which often result in excessive strain and injuries of the wrists or shoulders. Since wheelchair users are hardly able to do without their wheelchair in everyday life, these afflictions often become chronic. A group of researchers headed by Margit Gföhler, a specialist in biomechanics and mechanical engineering at the Vienna University of Technology, has now found a better alternative to the handrim in a project funded by the Austrian Science Fund FWF.
The most natural movement for the body
“When a wheelchair is driven by means of a handrim, the human body has to adapt to this simple mechanism. However, human joints are not really designed ideally for these movements,” explains Gföhler in the interview with scilog. According to her, more practiced wheelchair users particularly are prone to reaching far back on the handrim which requires extreme wrist bending. “Especially in extreme positions, this puts a great strain on the joints. The idea behind the project was to look at the problem from the flip side. We tried to find out what sort of drive mechanism would be most suited for the human upper body,” notes the researcher. The group not only relied on their own creativity, but also used computer simulations to find the optimum design. The only criteria were to avoid extreme body positions and to achieve the highest possible degree of efficiency. “Only then should you develop a mechanism that is adapted to the human body.” In order to identify optimal movement Gföhler's team created a simulation environment. “We used a musculoskeletal system of the upper extremity and then optimised the movement for maximum performance at minimum muscular effort,” explains the scientist.
Tests with prototypes on ergometers
The result of the computer simulation was an oval-shaped mechanism, similar to pedalling on a bicycle, a little further towards the front and a little further up than the handrim. The next step was to test the system. A prototype was built and installed on a wheelchair ergometer. “We carried out performance tests in which we were able to prove that this type of drive actually requires less power input than a handrim drive,” says Gföhler. One of the aspects the researchers measured in the test was the carbon dioxide content of the breathing gas under load conditions. The project partner for this step was the Weißer Hof Rehabilitation Centre, where the tests were carried out. Gföhler emphasises that similar systems already exist for the sports sector, so-called “hand bikes”: “Hand bikes use handles not unlike pedals for the hands. These systems are too unwieldy for everyday use, however.” Hand bikes are not suited for indoor use, for instance, and there are also differences in the sequence of movements.
Patent pending
One requirement for the prototype was that it must not increase the wheelchair’s width or length. This requirement has been fulfilled. Power is transmitted to the axle via toothed belts with only minor friction losses. According to Gföhler, the advantage of the better motion sequence greatly outweighs any disadvantages created by the belt. A patent has been applied for. The project was not only extremely successful from a scientific point of view, but the personal feedback of the test participants was also very good, reports the researcher. “It took a little time for people to get used to, but then they were all happy with it.” The researchers are now looking for business partners to develop a marketable product from the prototype.
Personal details Margit Gföhler is the head of the research group for Biomechanics and Rehabilitation Engineering at the Institute for Engineering Design and Logistics Engineering at TU Wien (Vienna University of Technology). After graduating in mechanical engineering, she obtained her professorial habilitation in the field of biomechanics, and her research focuses primarily on modelling the musculoskeletal system, motion analysis and assistance systems for people with disabilities.
Publications